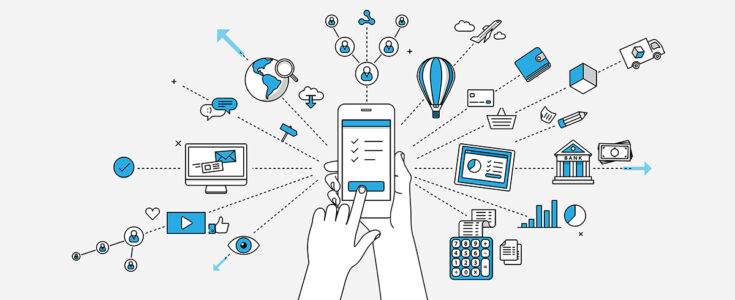
IoT & Manufacturing: Not Just for the End Customer
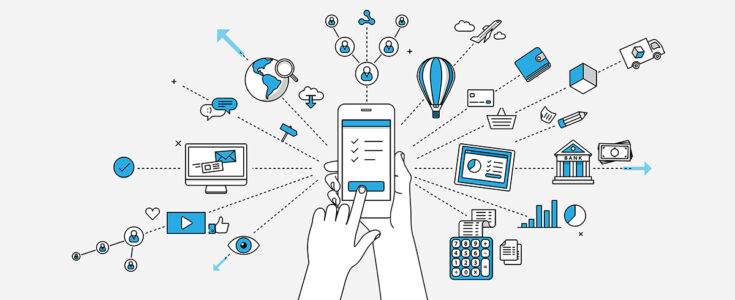
The Carrying Cost of Inventory
Connected devices are allowing companies to create new products for their customers and differentiate themselves against their competitors. However, don’t fall into the trap that IoT is just for your customers. Companies get so wrapped up with the customer, they forget that technology is out there to help them too.
Take a good look at some of the largest costs for operating your business in a new light. Is there a piece of information that would allow your company to be more flexible? Is there knowledge that would automate decision making? Is there information that would drive significant operational savings?
To help illustrate the idea that sometimes your company needs to look internally to help business, let’s take a deeper look at the carrying cost of inventory. Very often, inventory cost is one of the largest expenses and assets of an organization. It includes items like opportunity cost, physical space, insurance, obsolescence, employees… It’s a daunting list.
Manufacturers everywhere have their bottom lines continuously dragged down by the cost to carry old inventory. Most companies have a parts manager who has a fairly good handle on some of the popular items (at least we hope), but no visibility on the less popular parts. Inventory costs range, but typically it is around 20%-25% the value of that inventory. So how can your organization cut inventory cost in half?
It all starts with better information. That information is at the fingertips of manufacturers through the internet of things and connected devices. For a fun example, let’s say a company manufactures a product called “Product O.” It has $2,000,000 of parts inventory on hand and really wants to cut that down. So it starts connecting “Product O.”
Connectivity and technology are not the challenges. For this example we will say that “Product O” can connect to customers’ phones. As an incentive, the manufacturing company offered them an extended warranty if they registered online, named their local dealer, and connected their “Product O.”
Now the manufacturing company has information. They have a lot of information. They know how often Product O is in use, for how long, and when it is due for preventative maintenance. They know specifics… They know that three customers registered at a local dealer will need preventative maintenance within the next 45 days, based on their current usage. The manufacturing company can let the dealer know, get rid of the maintenance inventory, and, since they know how often “Product O” is in use, they might not need to replace inventory for a long time.
Furthermore, they will be able to see new trends in the data they are collecting. This will lead to new insight and allow them to accurately predict future inventory needs across many other parts. Since the data is continuously coming in, they will be able to adjust as needed. All this leads to cutting inventory costs.
Minimizing the carrying cost of inventory is just one example of internal IoT initiatives. Some other internal reasons for connecting devices are quality and performance, but the same connected device concept applies: Collect the data and do something with it.
Have questions on how to enable your products to connect? Contact our experts to learn more.