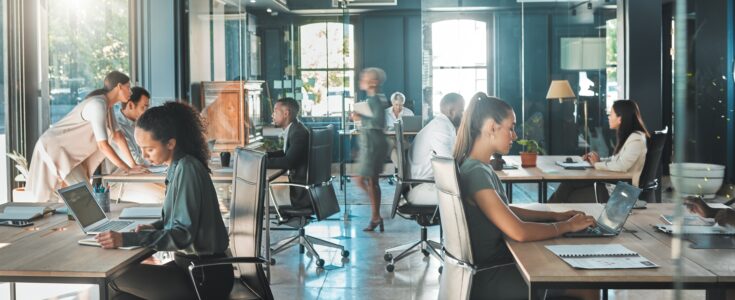
The Smart Workplace: How 3 Local Companies Are Using the IoT
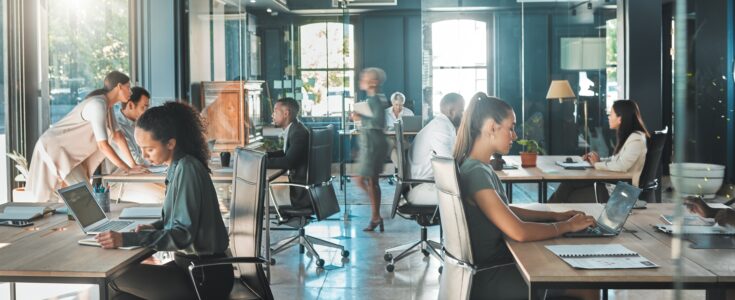
August 8, 2019
Via New IT Alliance
The Internet of Things (IoT) has made your home smart; you can program heating, lighting and security systems to automatically adjust themselves. You can program your Roomba to vacuum when you’re asleep. You can ask Google or Alexa to play the music you like when you come home. So why shouldn’t your workplace be smart as well?
The good news is that the workplace is smarter than it was a few years ago, but maybe not in the way you’d think. (Although companies like Amazon and Google are certainly betting on offices becoming just as smart and voice-activated as homes, the ubiquitous smart office is probably just a few years down the road.)
On the other hand, manufacturing industries have been putting the IoT to good use since it was first introduced. Sensors have transformed the industry and are helping make the factory floor one of the smartest workplaces around.
How manufacturers use IoT
In 2016, when the IoT was new, manufacturing was one of a handful of industries that had made significant investments in the Internet of Things. Today, most other industries are still quite sure what to do with it. According to a recent report from IoT Analytics, manufacturing is projected to be the largest market for IoT platforms by 2021, with an expected value of $438 million.
The manufacturing industry embracement of the IoT has happened for good reason — sensors attached to equipment, like pallets and machines, generate valuable data that help improve operating efficiencies, create safer environments for workers and tell technicians when parts need to be replaced.
This is the case at Appleton-based Miller Electric, the world’s largest manufacturer of arc welding equipment. At Miller Electric, IoT devices are hooked up to welding equipment., and those sensors produce a wealth of information. The sensors allow managers to track human welders’ performance, provide welding information to customers and track machine performance to see when a piece of equipment needs maintenance.
How other Wisconsin companies are using the Internet of Things
A Wisconsin-based naval ship building firm, on the other hand, has been using the IoT for safety purposes. The company puts chips in the helmets of its personnel, and those chips are read by a scanner as people walk on and off boats. This enables the company to know exactly where everyone is and can be used for safety procedures and measures. For example, if there is a fire on a boat the company would know immediately exactly who is on it and who is safe ashore.
An insurance company for jewelers based in Neenah, Wisconsin is more focused on using the Internet of Things to prevent theft. In 2016, the company displayed a smart jewelry showcase during the JCK Store of the Future Conference. While the smart display case was only in its concept phase, it contained sensors that detected patterns in movement, light, weight, temperature, humidity and pressure. If the sensors were to reach a certain threshold, they would then send notifications out to the staff, owners and appropriate authorities.
This data is able to tell jewelers if someone has been lingering nearby — or “casing the joint,” so to speak. Knowing this in advance helps jewelers know when to beef up security, or rotate merchandise in the cases to thwart a potential robbery.
In all three cases, the IoT helped workplaces become smarter, giving organizations the information, they need to improve efficiency, safety and security. However, businesses need more than sensors to effectively implement the IoT. This is because even though sensors do collect a large amount of data, unless there is a program in place to analyze the data, it is essentially useless.
What organizations need to get started with IoT
When it comes to the IoT, there are three important things to consider before an organization takes its first steps:
- Investing in a good AI (Artificial Intelligence)
- Security
- A plan for updates and upgrades
AI: In order to find patterns in the data and isolate the information that is most important to them, organizations must invest in good data analytics. By utilizing AI, or artificial intelligence, to help make sense of the constant stream of data produced by sensors and present it to stakeholders in an easy-to-understand format. That’s part of what Apexon did to help Miller Electric — Apexon partnered with Miller Electric to develop a custom cloud-based solution that transmits and analyzes welding data in real-time; allowing manufacturers to monitor productivity and quality standards while the welding is happening.
Security: Organizations also need to give some thought to security, because the IoT is technology and it can provide another entry point for hackers if left vulnerable. Any company considering the IoT will have to plan ahead to make sure their sensors are as secure as any laptop.
Upgrades: Lastly, organizations need to have a plan in place for how to update their IoT devices. Like all software, the code running on the machines will need regular updates, patches and upgrades. If this can’t be done in-house, that’s okay; technology consulting companies can help set up a plan.
Technology consultants can also help you design custom software for your IoT. For example, Apexon can help by creating an IoT process to fit your needs, connecting your current devices to one database, and displaying that data in a dashboard or a report. Apexon’s technicians have the expertise to use AI to automate the process. This would allow the system to generate alerts automatically, like in the case of the jewelry smart display, or to run steps that fix a problem. Finally, the information from the IoT can be automatically sent to other systems, software or applications, making your organization operate in a seamless, streamlined, and simplified manner.